
(4), when an electric field E is applied to a piezoelectric material. 6) (a) The electromechanical coupling factor k k 2 = (Stored mechanical energy / Input electrical energy) (4) or k 2 = (Stored electrical energy / Input mechanical energy) (5) Let us calculate Eq. 5) All are related to the conversion rate between electrical energy and mechanical energy, but their definitions are different. (ε : permittivity) (3) Electromechanical Coupling Factor k The terms, electromechanical coupling factor, energy transmission coefficient, and efficiency are sometimes confused. (2) Taking into account the relation, P = d X, we obtain an important relation between g and d: g = d / ε 0 ε. (1) Piezoelectric Voltage Constant g The induced electric field E is related to an external stress X through the piezoelectric voltage constant g (an important figure of merit for sensor applications): E = g X. 1-4) Piezoelectric Strain Constant d The magnitude of the induced strain x by an external electric field E is represented by this figure of merit (an important figure of merit for actuator applications): x = d E. In this chapter we describe the piezoelectric materials that are used, and various potential applications of piezoelectric materials. " Piezoelectricity is extensively utilized in the fabrication of various devices such as transducers, actuators, surface acoustic wave devices, frequency control and so on. The root of the word " piezo " means " pressure " hence the original meaning of the word piezoelectricity implied " pressure electricity. This is the converse piezoelectric effect. Materials showing this phenomenon also conversely have a geometric strain proportional to an applied electric field. This is called the direct piezoelectric effect and was discovered in quartz by Piere and Jacques Curie in 1880. The induced charges are proportional to the mechanical stress.
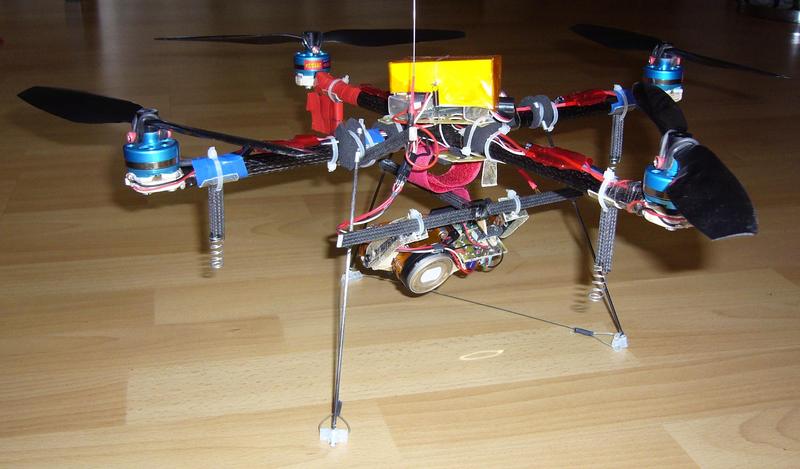
And even then, learn on a head holding gyro first, then progress onto the scale heli's and rate mode gyros.Certain materials produce electric charges on their surfaces as a consequence of applying mechanical stress. In conclusion, only purchase a head holding gyro unless you are wanting to go scale. It will also reset the gyros stored position to the new position you move your heli to. With a head holding gyro, the rudder signal from your transmitter no longer directly controls the tail – it simply tells the gyro how many degrees to turn per second. Heading hold gyros are very popular and pretty much standard among RC helicopter pilots for that very reason – they’ll hold your tail in a constant position no matter what you’re doing as long as you don’t input a rudder command, even if you’re doing 3D aerobatics or flying in a strong wind. Therefore, as you increase the throttle or headspeed of your heli, the head holding gyro will counter the main rotors thrust automatically keeping your heli’s tail in its original position. Based on the deflection from the set position, the gyro will control the rudder servo such that the gyro returns the helicopter to the set position.

In a heading hold gyro, a built microprocessor that keeps track of and remembers how far the helicopter has turned from its set position.
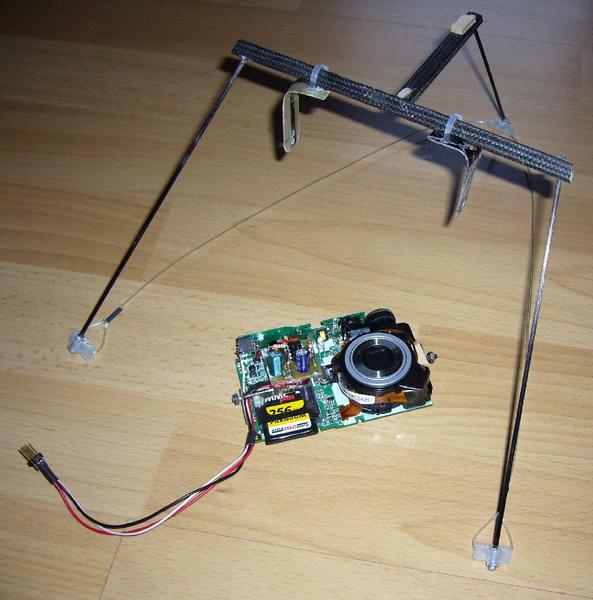
Heading hold or heading lock gyros are a conceptually simple extension of rate gyros. The reason for this, is that the servo will always go back to center when you release the stick. The only time that we will use rate mode on the gyro is when we are setting it up. Rate gyro’s are often used in scale RC helicopters because they lend themselves to a more realistic flying experience, while heading hold gyros are used by almost everyone else because they make flying easier.
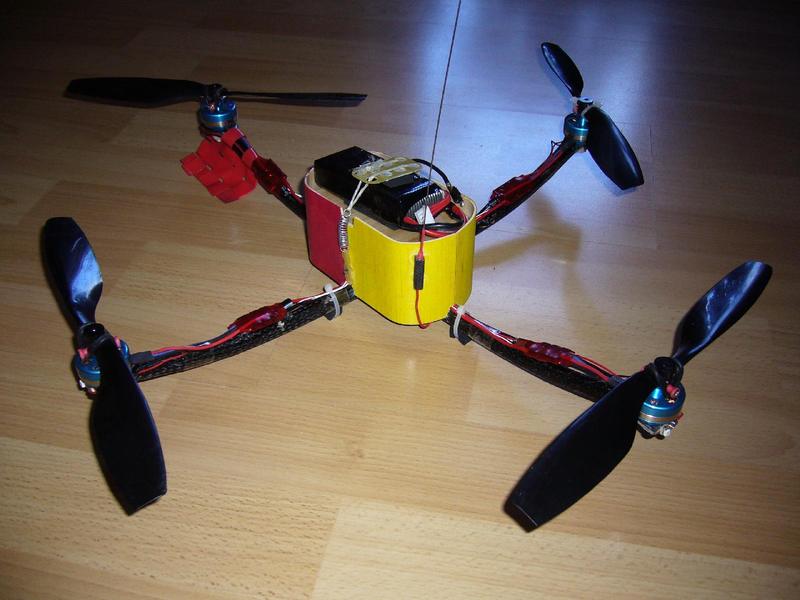
There are two types of gyro functions, rate mode and heading hold.
